Aseptic Services Manager and Deputy Associate Chief
The closing date is 18 May 2025
Job summary
An exceptional opportunity has arisen to provide leadership and quality sign off for the design, build and validation of a purpose built Paediatric Cancer and ATMP facility due to open at St Thomas' Hospital in September 2026 and once opened, to lead the core functions of the new unit and the existing Guy's Cancer centre chemotherapy and advanced therapy facility with overall responsibility for the services provided.
Main duties of the job
- To provide technical leadership for all aspects of the chemotherapy (including clinical trials) and advanced therapies services being provided from the St Thomas and Guys Cancer Centre and Guy's Pharmacy Containment Suite.
- To lead, deliver, develop and evaluate a comprehensive aseptic service including adult and paediatric chemotherapy, advanced therapies and aseptic manufacturing services to the Trust in accordance with the objectives set between the Chief Pharmacist, ACP Technical services and Clinical Pharmacy Services Cancer, Paediatrics and ATMP leads.
- To be responsible for strategic development of aseptic services within and external to the Trust in line with regionally and nationally agreed NHS priorities
- To be responsible for the research and development program within aseptic services ensuring that projects are identified, delivered and documented within an agreed time frame in collaboration with the clinical trials teams.
About us
Join Us at the Forefront of Innovation in Cancer & Advanced Therapy Care!Pharmacy Aseptic Services - Guy's & St Thomas' NHS Foundation Trust
We're embarking on a groundbreaking journey--and we want you to be a part of it.
Guy's & St Thomas' is building a brand-new, state-of-the-art Pharmacy Aseptic Unit at our St Thomas' site, purpose-built for the preparation of chemotherapy and cutting-edge advanced therapies. This is more than just a project--it's a transformation that will shape the future of patient care.
Why Join Us?
- Be at the centre of innovation: Play a vital role in designing and launching a modern aseptic facility.
- Drive real impact: Your expertise will directly contribute to improving outcomes for patients requiring highly specialised treatments.
- Work with the best: Collaborate with leaders across pharmacy, clinical services, procurement, finance, and Trust management.Shape the future: Influence every stage--from specification and validation to full operational delivery--with quality and patient care at the heart of it all
What You'll Be Doing:
- Leading on technical aspects of the new unit's design and operation.
- Ensuring full compliance with regulatory and quality standards.
- Being a key voice in a cross-functional project team to create a facility that is future-ready.
- Helping to deliver a unit that reflects the evolving needs of modern medicine.
Details
Date posted
25 April 2025
Pay scheme
Agenda for change
Band
Band 8c
Salary
£82,462 to £93,773 a year per annum incl. HCA
Contract
Permanent
Working pattern
Full-time
Reference number
196-SMT1717
Job locations
St Thomas Hospital
Westminster Bridge Road
London
SE1 7EH
Employer details
Employer name
Guy's and St Thomas' NHS Foundation Trust
Address
St Thomas Hospital
Westminster Bridge Road
London
SE1 7EH
Employer's website
https://www.guysandstthomas.nhs.uk/careers/careers.aspx (Opens in a new tab)

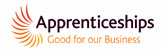

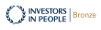
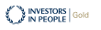
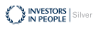
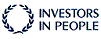





Employer contact details
For questions about the job, contact:
Supporting documents
Privacy notice
Guy's and St Thomas' NHS Foundation Trust's privacy notice (opens in a new tab)